MANAGEMENT SOFTWARE FOR TEST BENCH
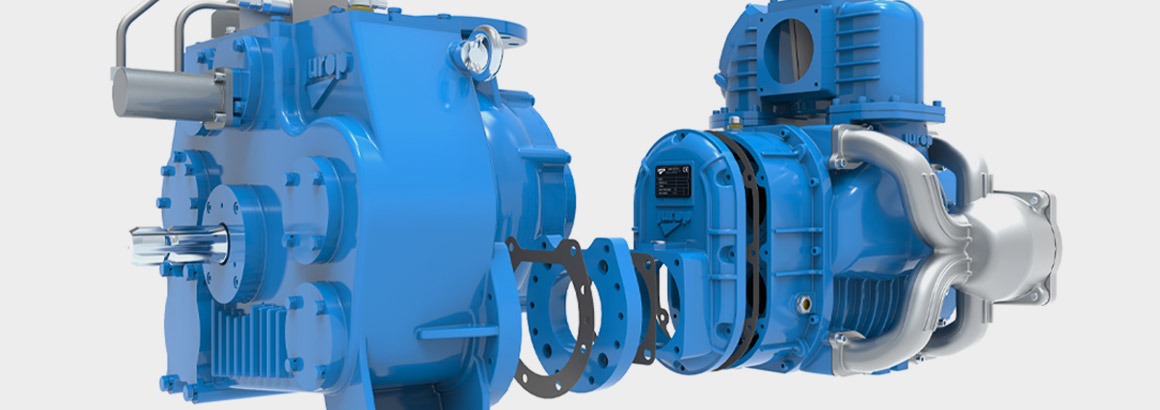
Reviewing the test bench to test and measure the performance of products such as vacuum pumps and compressors. The intervention required the development of a new centralised system for data management and improvement in the automation of the test system. Positive and stable effects on R&D, sales and testers.
MAIN CHALLENGE
To optimise the testing process, in addition to improving the control system and the functions of the test bench, a new data management structure had to be organised, both for those requested in the input phase and those generated as output. We therefore implemented the database architecture, the interface software for its consultation for the technical office, for the commercial one and for the testing department, and the integration between this database and the testing software itself. In order to be efficient, the automation of the process thus configured has entailed the introduction of new procedures and best practices, therefore of habits to be acquired, a delicate choice. However, given the achievable results, any hesitation regarding the change has disappeared.
CUSTOMER COMPANY
Jurop S.p.A. designs and manufactures vacuum pumps, compressors, suction units and equipment built on chassis, trailers and semi-trailers in a fixed or drive-over way to vacuum, collect and transport liquid waste. It addresses the industrial sector, the agricultural sector and municipal companies in over 80 countries around the world.
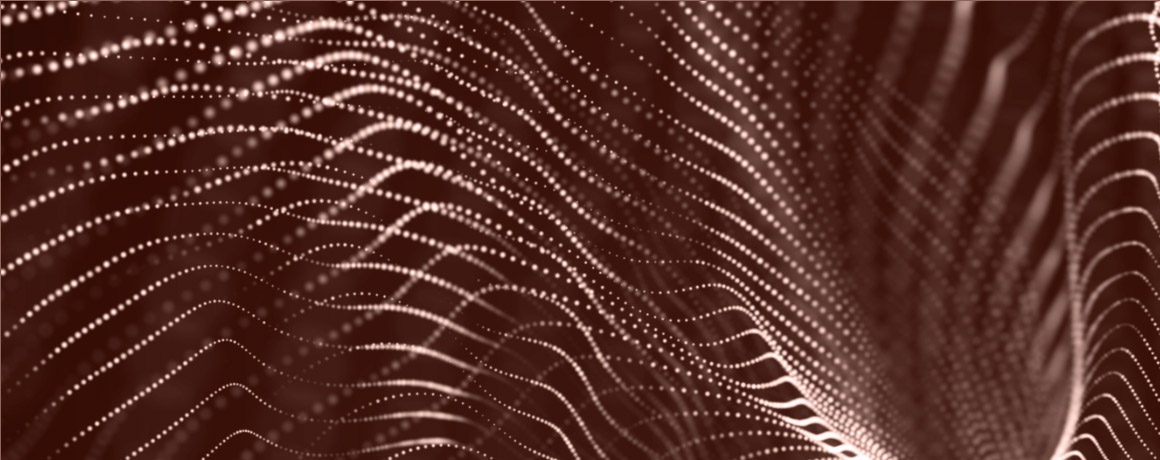
OPERATION
The centralised system built to manage test and inspection benches is based on a database with the entire product catalogue and related test data. More precisely, it includes all the technical information of the products, the tests necessary for each and the results, and is related to the software interfaces for communication between people, machines and the database itself. It can therefore be automatically implemented and is automatically available with incoming and outgoing data, even in the form of PDF reports, depending on the needs of people who perform different business functions. It eliminates the possibility of error in the communication of data and in their storage compared to non-centralised and automated methods.
The test bench management software for vacuum pumps and compressors implemented for Jurop is a versatile tool. It allows multi-user and multi-purpose access: it is used to test products in the design and construction phase by the R&D function or in the testing and maintenance phase for technicians or to find performance information, useful for salespeople to acquire customers.
Using the new test bench management software, the technical office establishes the correlations between the product catalogue and the testing methods to which each individual item is subjected, after all it works automatically. The software acquires the data, automates the bench, performs the test, saves the results in the database, generates the report on what has been done, sends it in PDF format to those who have requested it and stores it in a secure, stable and always accessible way. The research tests are so easy to conduct and repeat. Because they do not require supervision, technicians have more time to dedicate to higher added value activities.
Thanks to the centralisation of all the test data and the dedicated interface, today salespeople know where to find this information without fail, can consult it immediately and autonomously, and have the certainty of its organic and orderly filing. It is therefore a considerable simplification of their activities and a single and structured source regarding the performance related to product testing tests, sales ideas and forecasts of the behaviour of the machines.
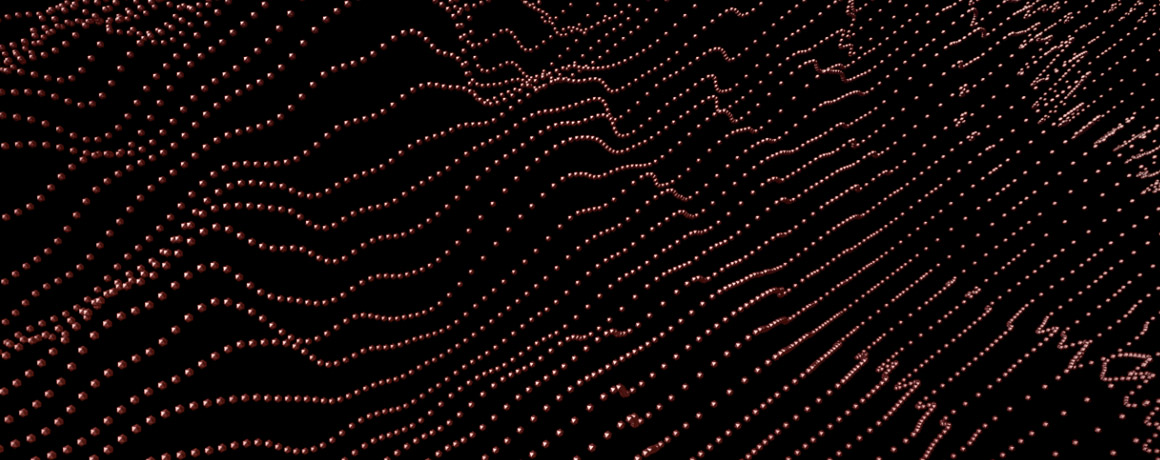
SERVICES
ADDED VALUE
The added value of the management software for the test bench lies in having integrated the automation of the rig with the centralised database of both input and output data. This has changed the handling of internal data. Today they are completely digitalised, the process is completely automated, and the information is now computerised with work points that were not possible before.
SERVICES
WHY STREAM
The difference we can offer in software customisation depends on the vertical know-how in thermo-fluid dynamics that we have in Stream, pursued since the university laboratories and then continued with measurements and experimental activities in the industrial field. For example, by customising a measurement software, developing a thermodynamic model to predict the operation of a machine, identifying how to improve the performance of a product or building a configurator. It is this vertical knowledge of thermo-fluid dynamics, put to the test every day, that makes the difference: it increases sensitivity for the elements to be analysed, the calculations to be tested and those to be ignored.
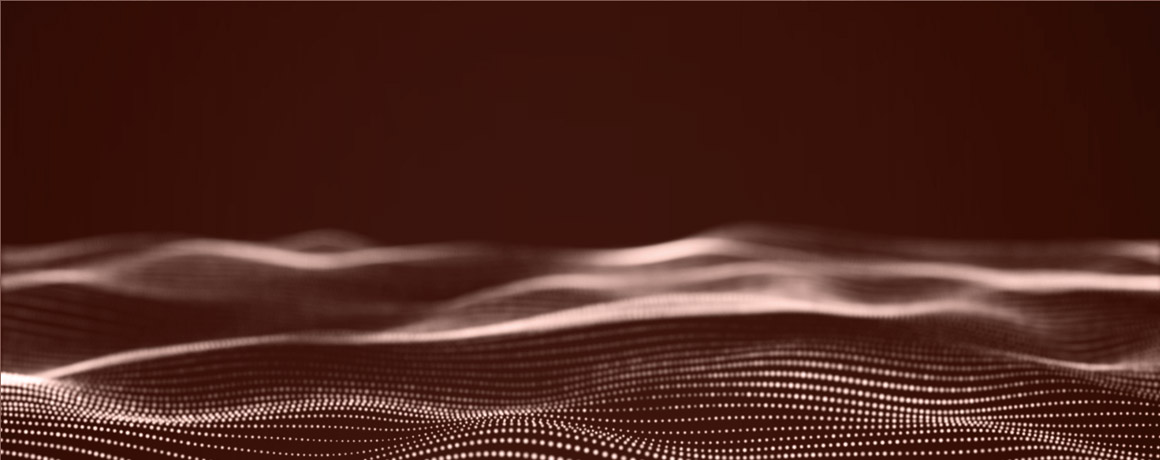
MODEL YOUR FUTURE!
FOR THE MANAGEMENT OF TEST BENCHES
We are always ready to discuss how to customise a software for the management of testing systems, making our vertical skills in thermo-fluid dynamics available. They make a difference. Our background of experiments and vertical studies on the subject, has made us develop particular sensitivity as well as making us embrace each project also looking at spin-offs useful for future activities to optimise the performance of products and the technical organisation of connected data.
Let’s talk about it, request a phone call for some knowledge.
STREAM SRL
Via Sondrio 1, 33100 Udine – Italy
[+39] 0432 46639
Monday – Friday 9 a.m.- 6 p.m.
info@streamengineering.it